There are many advantages of using TITAN servo controllers with conventional motors such as brushed DC motors. Setting up a motor with the TITAN software is an easy process that you should be able to complete on your own by following these simple steps.
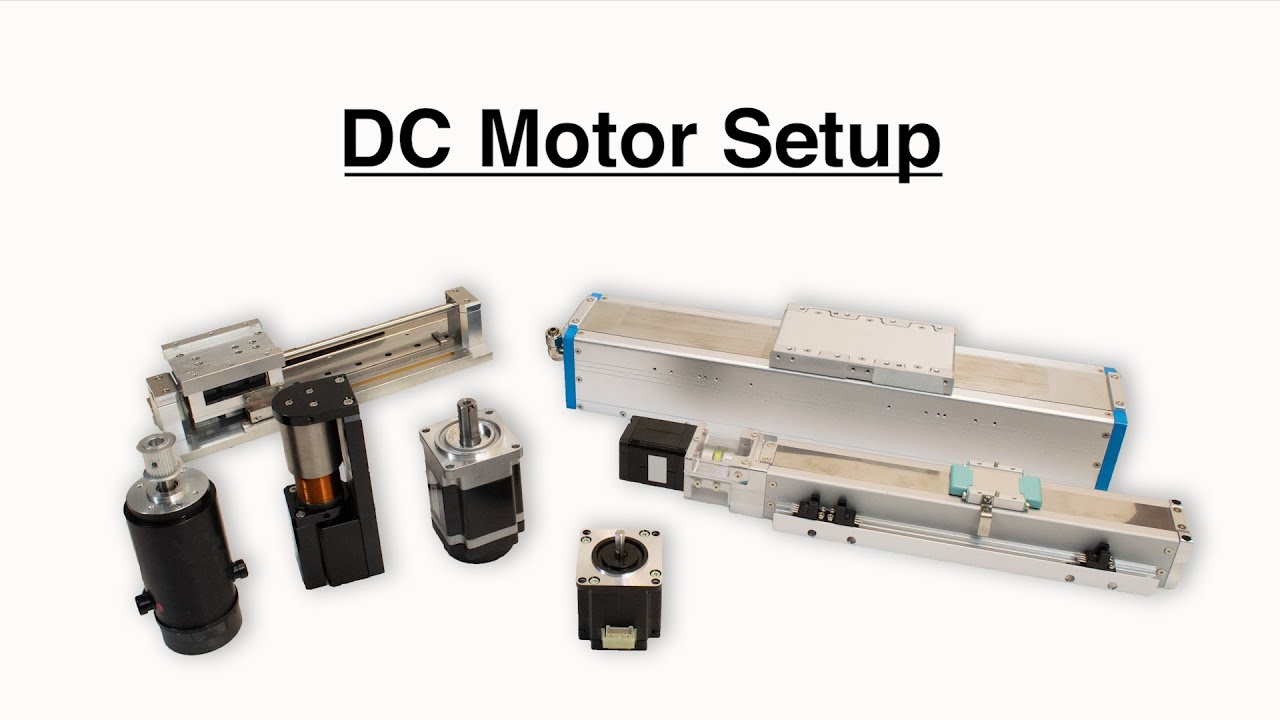
First, connect the DC motor, power up the motor controller, and open the TITAN software. Check the USB communication by navigating to the "Communication" window and clicking "Check Communication". Close the window and return to the homepage.
Next, go to the motor setup window. Check the encoder resolution of the motor by clicking the encoder check button. You can manually rotate the motor shaft to see that the encoder count is changing. Turn the motor several times and you will also see the encoder resolution value.
Once you have confirmed the encoder is working, open the motor database wizard. Click consent and go the next screen Your screen should look something like this:
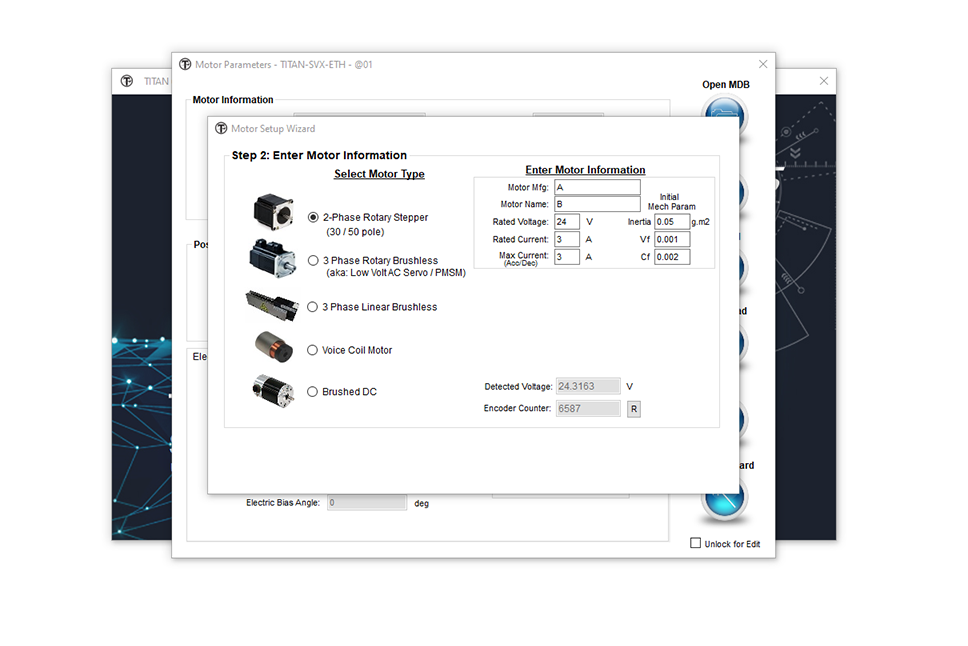
Select the "Brushed DC" motor type and input the manufacturer, motor name, voltage, rated current, and max current for your brushed DC motor.
Now we can perform the auto detect routine to determine the motor parameters. The encoder count resolution is determined using the encoder index channel. If there is no index channel, you will need to manually input the encoder resolution.
Next, the motor electrical and motor mechanical parameters are determined. Save the parameters to the database file so that we can reuse the database when using the same motor with other TITAN controllers.
To test the motion of your brushed DC motor, go to the test drive window and enable the motor. You can see that the motor is enabled and in position. Here, you can try different jogging or positions moves to test the motion of the motor. See our detailed guide on using the test drive HERE.
Once you attach a load to the motor, you will want to tune the system parameters from the tuning window. To learn how to do this, see our guide on HOW TO SET UP A BALL SCREW STAGE.
If you go to the configuration window, you will see various configuration settings. In the parameters window, you will see a full summary of the motor setup which includes the motor database values and the full system configuration values.
Once everything is done, a store to flash can be performed to save all settings to the motor controller. You can also save the system settings to a file so that they can be loaded to another TITAN controller with the same setup.